EPS foam, or rather, expanded polystyrene foam, is commonly known as the trademarked styrofoam made for thermal insulation and craft applications. EPS is a lightweight, rigid, and closed-cell form that blocks water and vapour from interacting with the outside elements.
As EPS is used in various industries, including packaging, shipping, mould-making, and theming, heavy research was poured into optimizing and perfecting the processes. Arriving from a two-stage synthesis, raw polystyrene beads are expanded using steam to create pre-puff beads that are then further steamed to create the iconic block that is seen everywhere. EPS is especially attractive due to its green nature. It does not produce any carcinogenic organic substance during production at all. Further recycling procedures have also been introduced to ensure the reusability of the foam after use, and foam produced from mushrooms is starting to become popularized!
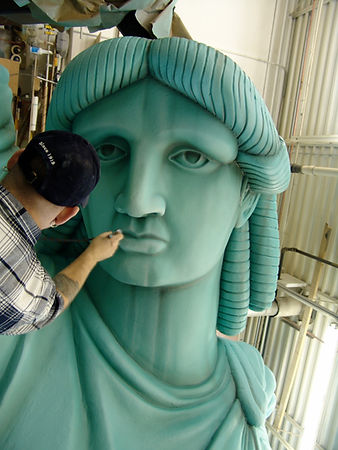
With EPS, Streamline Automation suggests a Hotwire cutter like the FROGWire™ to take advantage of its ability to process large blocks of foam as a whole, rather than breaking up the job into several smaller jobs. Other materials that are denser cannot be cut in this manner and will require specialty saws or alternative tools. In addition, our FROGMill™’s 4th extended axis is able to fit parts as large as 48’’ in diameter and 8’ in length to be machined. Any other material of this size would be a tremendous challenge to work with due to the potential weight, limitation of tools, thickness, and fit of the material. EPS, on the other hand, is the only acceptable material at this rate to be handled and worked in this capacity.
All in all, EPS is an ideal material to work with for prototyping due to its versatility, light-weight nature, and ease of use. With the different FROG3D® systems, we hope to provide you with the ability to produce projects you’re passionate about. Reach out to us and see how the different EPS uses can open new markets and allow you access to different clients today.