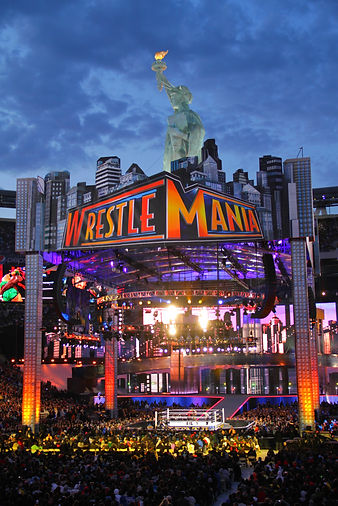
As the world moves toward automation, rapid changes in various industries have created the race to adapt to the incoming technological advancement available. On the market today, there are big and small improvements that have been found to make production more simplified compared to a mere half a decade ago. We’re really entering unprecedented times in terms of upgrades and gadgets. In the machining world, better drive systems, motor capacities, and gear tolerances are all receiving their respective tune-ups. Heck, even data transfer cables that signal motors are more efficient as manufacturing processes advance. So, the question is: when is the right time to switch out the old and bring in the new? Is the cost-benefit of a new machine really worth it to be swapping out slightly older models? As an automation solutions provider, Streamline Automation is always ready to answer your questions and address your curiosities.
Generalizations aside, what are some of the most important upgrades you can receive by switching your equipment today? When someone shops for new systems, it’s always good to consider two separate but intertwining components: the hardware and the software. What are some of the hardware pieces that you can’t live without nowadays? Also, why is upgrading software so important in this day and age of the machining industry?
When we speak of software upgrades, this relates to the software that comes with the machines themselves. At Streamline Automation, we equip different software to better accommodate different machines, allowing them to target specific applications and ease the learning curve for incoming users. Changing software can introduce new functionalities in an existing system, unlocking new applications that may not have been previously achievable. For example, our in-house software FROG4D™ was developed to address the complicated indexing functions on particular 4-axis machines. This way, we don’t have to manually resort to programming each individual project that requires 4-axis machining.
Compared to software upgrades, hardware is not updated as often. Hardware most often consists of mechanical upgrades to current systems. Most of the time, hardware upgrades are needed when outdated systems cannot keep up with current software and thus experience compatibility issues. We recommend looking for hardware replacements when essential components like motors or control software are no longer available for replacement. At times like these, it’s usually simpler to look for a trade-in of the old system instead of searching the internet for the rare components. Other times, newer hardware technologies like motors aren’t compatible with older wiring harnesses and will require replacements that aren’t supported on the main controller software. It’s always a good idea to stay up-to-date with the emerging technologies while at the same time being diligent in studying the actual upgrades that new systems can provide. We all know that the shiniest machine in the shop might not be the best one for you.
If you’re ever confused or want more information about different automation systems, we can help you with potential upgrades and technical support that can boost production. We use the most up-to-date components that are available at the time of design to outfit your shop lineup. To learn more about how Streamline Automation may help you, contact us today.